Introduction
Mass flowmeters are essential for quantifying fluid and gas flow in industrial settings, renowned for their precision and dependability.
This guide provides an in-depth look at mass flowmeter technology—from Coriolis to thermal—detailing how these instruments are used to achieve accurate measurements critical for process optimization and commercial transactions.
Exploring the Essentials of Mass Flow Meters
Mass flow meters are designed to measure mass flow, indicating the mass rate at which fluid passes through a fixed point within a tube and thus quantifying the quantity of fluid moving through the system. This mass flow rate is distinct from the volumetric flow rate, which quantifies the volume of fluid flowing per unit time.
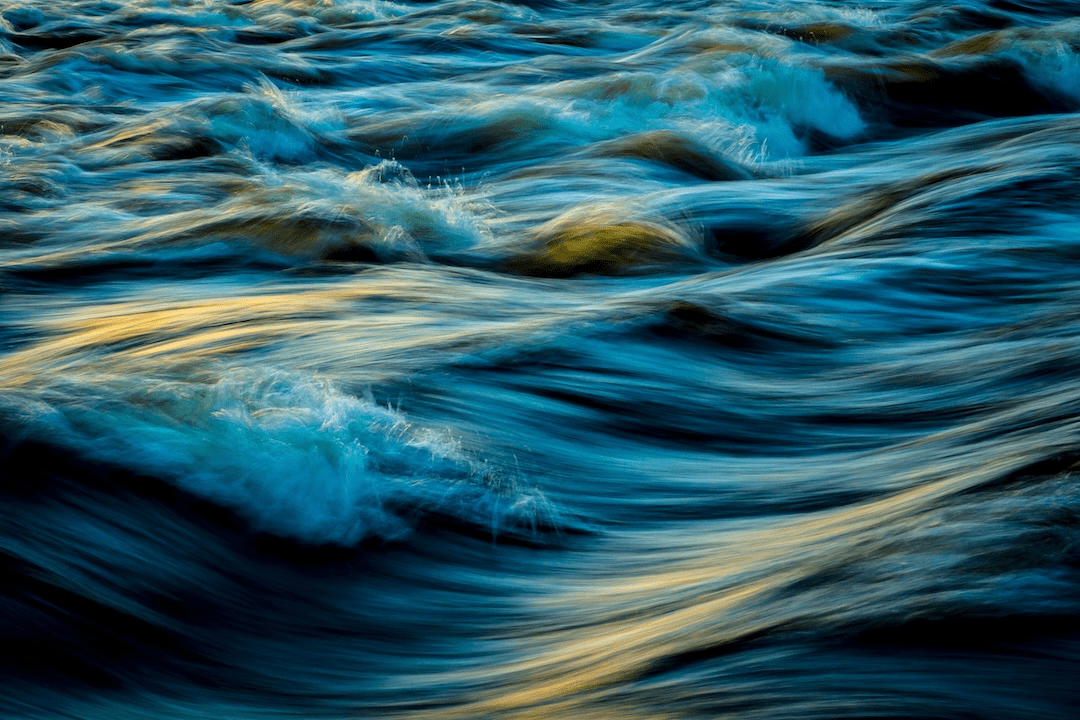
What sets mass flow measurement apart is its resilience against changes in fluid density. Mass flow measurement provides a consistent and reliable metric for the quantity of molecules in the fluid flow, irrespective of pressure or temperature conditions.
The Principle Behind Mass Flow Measurement
Historically, mass flow was estimated by reading volumetric flow meters and then calculating for density, but this method lacked precision. With the advent of modern technology, advanced methods have been developed for mass flow measurement, including the use of a volumetric flow meter.
These methods evaluate the quantity of substance passing through a meter within a specific time period. One such method is the use of twin turbine mass flow meters, which exploit the principle of fluid inertia involving the motion of twin turbines with variable blade pitches to determine mass flow rates. Another popular option is the use of magnetic flow meters, which are known for their accuracy and reliability.
Direct Versus Indirect Mass Flow Monitoring
While indirect methods of mass flow measurement incorporate volumetric flow and density measurements to infer mass flow, they can be prone to inaccuracies due to changes in temperature, pressure, and density.
Conversely, direct mass flow meters like Coriolis or thermal mass flow meters measure the mass flow rate directly through direct mass flow measurement, eliminating the need for separate calculations or dependence on external measurements, thus significantly improving accuracy.
Unveiling How Mass Flow Meters Operate
Ingeniously designed, mass flow meters integrate temperature sensors and advanced flow technologies to determine the flow rate of fluids and gases. They employ principles such as the absorption of heat by the fluid or the Coriolis effect, a phenomenon in fluid dynamics where a fluid’s flow path becomes curved in a rotating system.
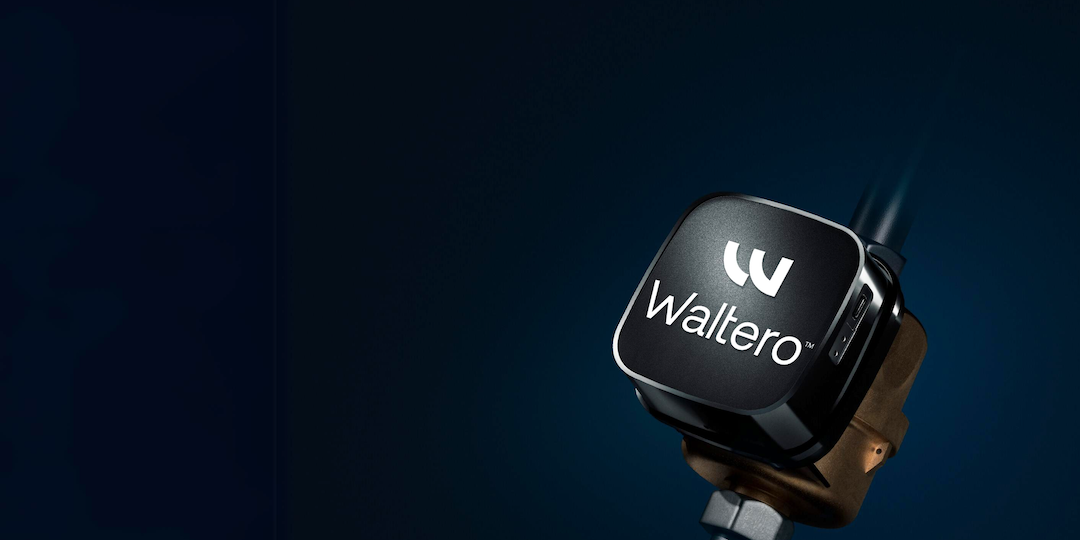
But like any other precise instrument, mass flow meters require proper installation for optimal performance.
This includes installing the meters in uninterrupted pipelines and maintaining regulated distances before and after the flow meter to ensure accuracy.
Coriolis Flow Meters: Harnessing Fluid Dynamics
Coriolis flow meters are a marvel of modern engineering. Their operation principle relies on the fluid-induced forces and resulting deflection of a vibrating tube. The Coriolis mass flow rate is determined by the phase shift between two sensors on the vibrating tube, where the magnitude of the shift reflects the flow rate.
In addition to mass flow, a Coriolis meter is also capable of independently measuring the fluid density by observing the frequency of the tube’s vibration, where denser fluids vibrate at lower frequencies.
Thermal Mass Flow Meters: Utilizing Heat Transfer
While Coriolis meters rely on the principles of fluid dynamics, thermal mass flow meters take a different approach. They estimate flow rate by introducing heat into the fluid and measuring temperature variation, or by maintaining a probe at a constant temperature and measuring the energy required.
Temperature sensors in these meters detect the temperature differential resulting from the heat transfer to the flowing fluid, and the mass flow rate is determined by either the power applied for heating or the temperature difference between sensors. This makes thermal mass flow meters particularly suitable for gas measurements.
The Spectrum of Mass Flow Meter Types
The diverse array of mass flow meter types caters to the unique demands of varying applications. These include:
Coriolis meters are known for their high accuracy and fluid density measurements
Ultrasonic meters that use sound waves for non-invasive flow measurement, offering an edge for corrosive and abrasive fluid streams
Oval gear flow meters designed for high-viscosity fluids
Impeller turbine flow meters utilize both a turbine and an impeller to interact with the fluid stream, providing measurable outputs of mass flow.
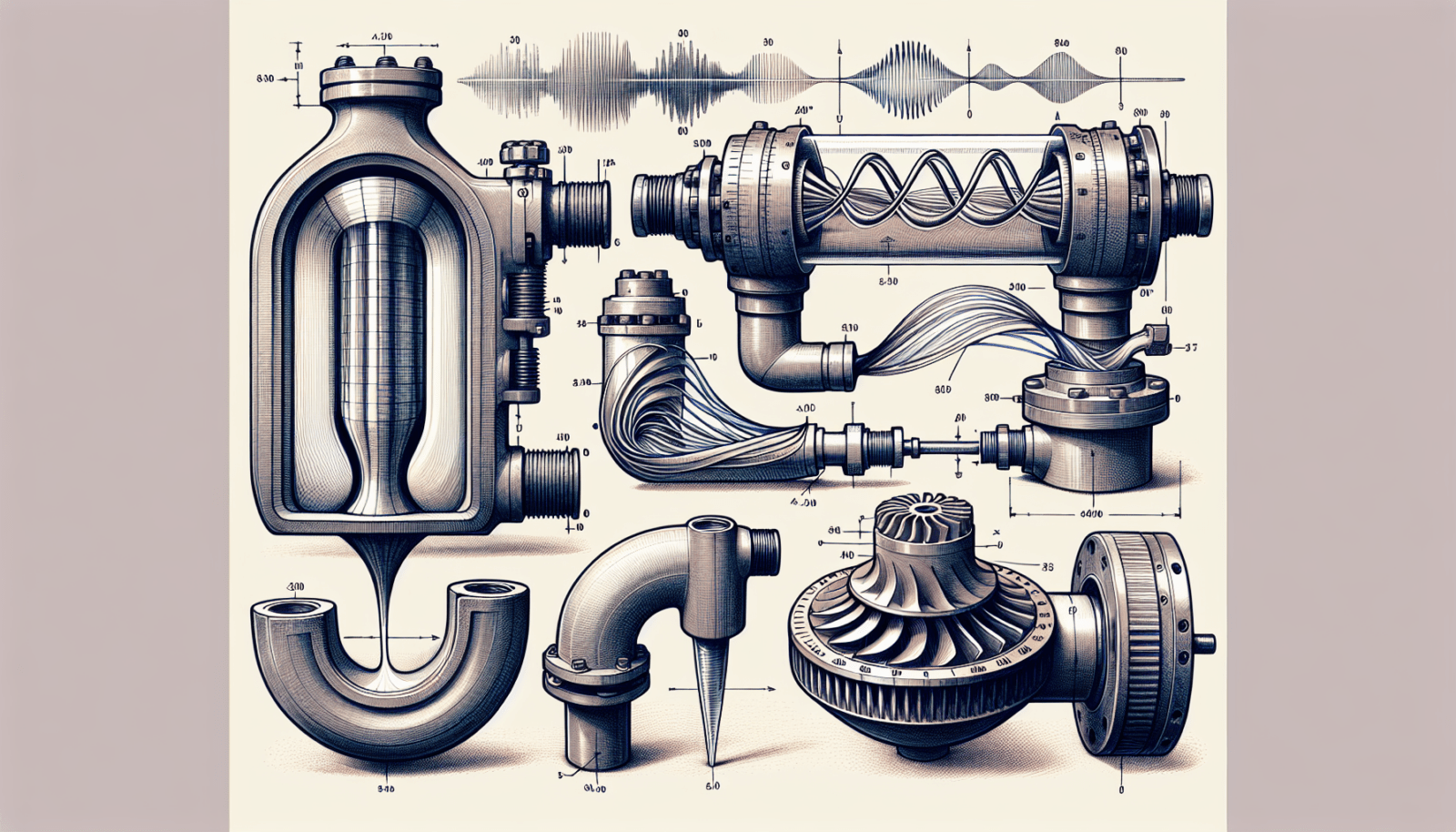
Ultrasonic Flow Meters: Non-Invasive Flow Technology
Ultrasonic flow meters offer a unique, non-invasive method for measuring flow rates. They use acoustic vibrations or sound waves to measure the flow rate of liquids and are particularly useful in applications involving wastewater or dirty conductive liquids. The ultrasonic flow meter measures these rates accurately and efficiently.
These meters are often employed in applications that require a certain degree of delicacy, such as the handling of corrosive liquids, as their design allows for the measurement of flow rate without any direct contact with the fluid.
Measuring Up: Mass Flow Meter Accuracy and Precision
Accuracy and precision hold paramount importance in mass flow measurement. The inherent deviation margin defines the accuracy of mass flow meters, indicating a possible difference between the actual flow rate and the one displayed by the meter.
Repeatability, on the other hand, refers to the instrument’s ability to produce consistent results under stable conditions, which is crucial for their precision.
The resolution of a mass flow meter determines its smallest measurable increment, directly influencing the precision and accuracy of flow measurements.
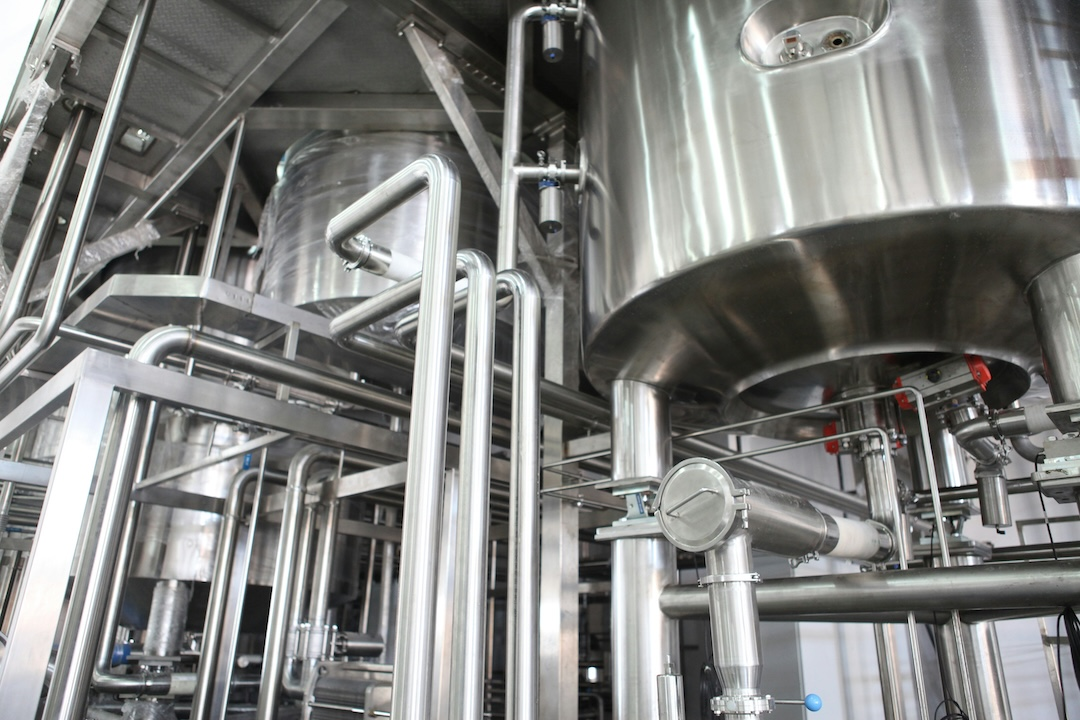
Factors Influencing Flow Meter Performance
Flow disturbances such as elbows, valves, and fittings can disrupt the flow profile, leading to imprecise mass flow meter readings. In such situations, flow conditioners are used to normalize the flow profile when a sufficient straight pipe run is not possible.
Additionally, in thermal mass flow meters, the presence of moisture or particulates in the gas can impact measurements by influencing the heat transfer characteristics around the sensor.
This necessitates the careful selection of the installation site for a thermal mass flow meter, as installation-related flow disturbances can result in reading inaccuracies.
Adherence to the manufacturer’s installation guidelines is vital for maintaining the precision of mass flow meters, where failing to comply can significantly degrade accuracy.
Ensuring Accurate Measurements
Maintaining the accuracy of mass flow meters necessitates regular calibration in adherence to the manufacturer’s guidelines. Typically, manufacturers advise on the frequency of calibration required to uphold the accuracy of their mass flow meters. Verification procedures may involve comparing the mass flow meter’s readings against a known standard to ensure consistency.
For thorough accuracy verification, mass flow meters can be sent to the manufacturer’s facility or to an authorized independent service provider.
Practical Applications of Mass Flow Meters
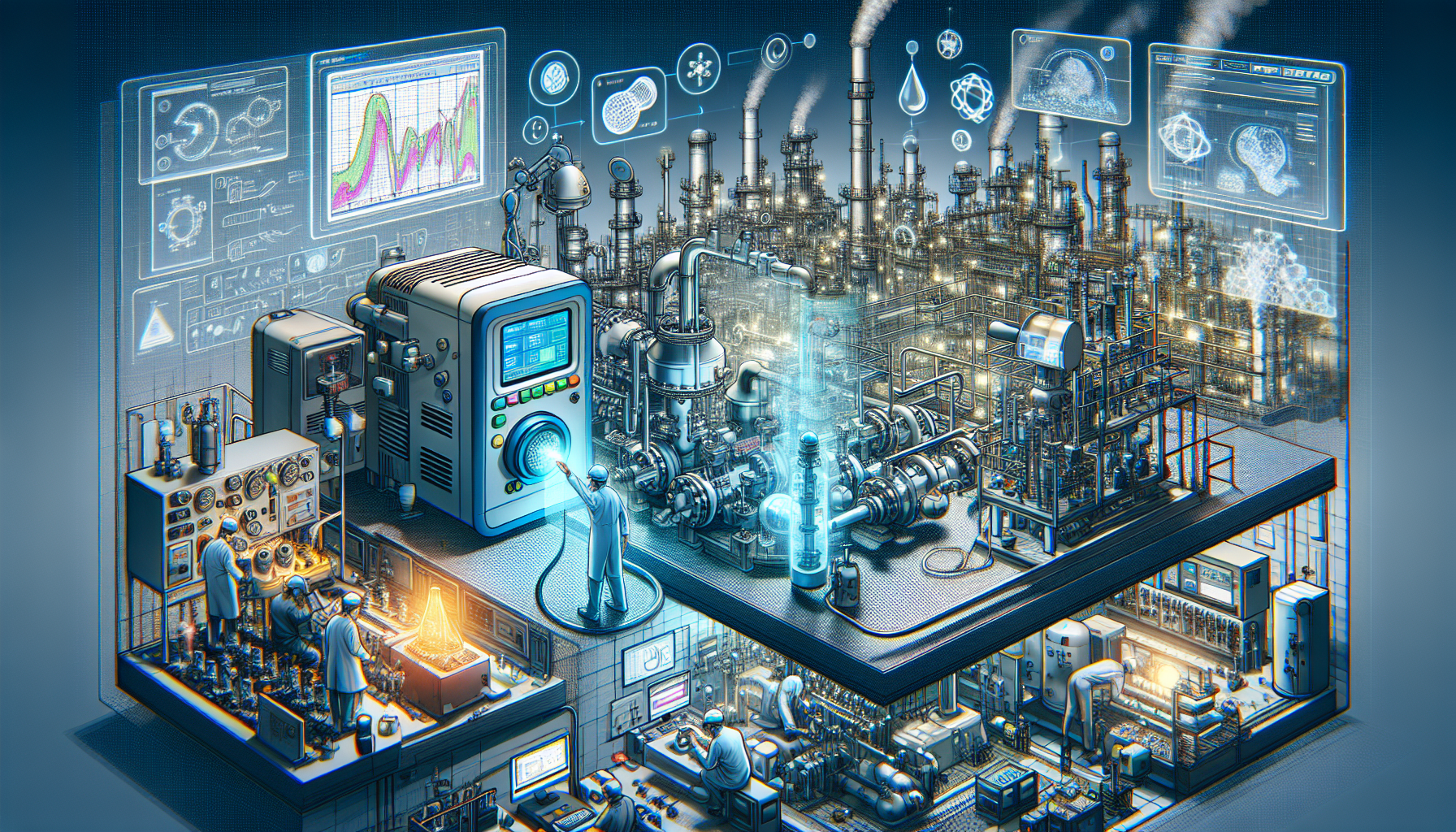
Mass flow meters are not just remarkable pieces of technology; they have practical applications across various industries. They play a crucial role in ensuring the accuracy of recipe formulations and material balance calculations in industrial process control, and are key to financial operations such as billing and custody transfer.
Thermal mass flow meters, in particular, are vital for precise gas flow control in semiconductor manufacturing, combustion air measurement for boilers, and gas chromatography.
Industrial Process Control
In industrial process control, mass flow meters play a key role in managing and monitoring material flow, leading to enhanced precision in batching, measurement, and defect detection. Industries such as food processing, pharmaceuticals, petroleum refining, and chemical manufacturing heavily rely on mass flow meters for the precise measurement and control of their materials, with Coriolis meters being particularly favored in applications demanding extremely precise mass flow measurements. Read more on industrial flowmeters here.
Specialty Gas Handling
Coriolis meters are widely used in various applications, including:
Industrial process control
Managing the delivery of industrial gases
Handling varying or unknown gas or liquid mixtures
Measuring supercritical gases used in several industries
Their versatility and accuracy make them an asset in specialty gas handling.
Addressing Common Challenges in Mass Flow Measurement
While mass flow meters offer numerous advantages, their usage also presents certain challenges. For instance, air bubbles in the fluid can disrupt the operation of Coriolis meters by impacting the tube’s vibration, resulting in inaccurate mass flow readings.
Another challenge is the fluctuations in velocity due to pulsating flow in systems, which can lead to measurement errors by causing variations in the flow rate readings.
Mitigating the Effects of Environmental Variables
Minimizing the impact of environmental variables plays a vital role in securing accurate mass flow measurements. Temperature compensation in mass flow meters is vital for providing accurate measurements under fluctuating temperature conditions.
To counter this, advanced mass flow meters incorporate real-time temperature data to adjust the flow measurements dynamically, addressing the thermal expansion or contraction of fluids.
External vibrations can also lead to inaccuracies in mass flow readings, especially when they interfere with the sensors’ ability to detect subtle changes in flow.
To mitigate this, flow meters often incorporate vibration-damping materials and mounting techniques to isolate the measurement system from any external vibrations.
Conclusion
In conclusion, mass flow meters are a cornerstone of modern industry, offering a reliable and precise method for measuring the flow of gases and fluids. Through the principles of thermal dynamics and the Coriolis effect, these devices can directly measure mass flow rates, providing an edge over traditional volumetric flow meters.
The array of mass flow meter types, including Coriolis and ultrasonic meters, caters to the unique demands of various applications, ensuring that regardless of the industry or the fluid in question, there’s a mass flow meter that fits the bill.
However, while mass flow meters are impressive devices, their accuracy is influenced by several factors, including installation conditions, temperature and pressure fluctuations, and the presence of air bubbles or pulsations in the fluid.
However, with regular calibration, adherence to manufacturer guidelines, and the use of flow conditioners and temperature compensation mechanisms, these challenges can be effectively mitigated, ensuring the longevity and accuracy of the flow meter.
Whether in industrial process control, specialty gas handling, or in countless other applications, the value of mass flow meters is clear. As technology continues to evolve, these devices will undoubtedly become even more precise, more versatile, and more integral to the operations of industries worldwide
.